Schedule
TIMELINE / FALL QUARTER / DESIGN:
The timeline for this project is one full school year at Central Washington University. The school year began mid-September and included three quarters those of which are ten weeks each. The entire project will be wrapped up in the first week of June. The first quarter of the school year is dedicated to the design and analysis of the device and has a deadline of mid-December. The first quarter included doing such work as the project proposal, analyses, and documentation. In Figure 7, attached below, the Gantt chart schedule for this project can be found. This chart shows the first quarter spanning from September to December, the tasks completed, and the time each task took.
​
When in the design phase, things do not always go as planned. The Gantt chart is meant to be a framework of the expected schedule of the project, but many factors can have an impact on the schedule. Such things as workload in other classes, family emergencies, and just lack of proper planning. This project was victim to all three of these factors. To battle these inconveniences, late nights, taking advantage of mentor hours, and zoom calls with professors helped immensely. There were also a few schedule mishaps when tasks took longer than expected. Some of the tasks that took longer than expected were tasks 1a and 1b, the introduction and the analysis writing portion. These presented difficulty in the way that the project was just getting started and a lack of understanding of the expectations led to a lot more hours spent than intended. Some of these hours included research.
WINTER QUARTER / CONSTRUCTION:
Construction occurred during winter quarter (January-March). Tasks handled during this time included purchasing parts and materials to then manufacture to assemble the device. Quite a few parts for this project were purchased as McMaster-Carr has a lot of options for conveyer components. Some of the parts purchased were, roller mounts, 4-bolt ball bearings, head pulley, key stock, AC gear motor, etc. All these parts were assembled to construct a conveyer system. Some of the manufacturing that was done things such as cutting the key stock with the vertical bandsaw, punching holes with a turret punch, bending sheet metal with a break, using the drill press to make fastener holes, cutting shafts to appropriate lengths, and broaching keyways. All of these tasks can be found on the Gantt chart below in sections 4 and 5 (part construction and device construction).
Similar obstacles that were faced during fall quarter were also faced in winter quarter. Time management was key, but sometimes this wasn't enough. A few of the parts that were intended to be ordered were 6-7 weeks out and would not fit the schedule laid out for the quarter, so alternative plans needed to be made. For example, the head pulley with the keyway would not arrive on time. To mitigate this issue, a straight pulley, keyway broach, and broach collar were purchased to ensure that a pulley with a keyway was constructed before the end of the quarter (project deadline). This extended the time anticipated to be spent on construction but ultimately worked out and a working device was assembled. In addition to this, in the last week of manufacturing when trying to assemble the belt, it became clear that a tensioner was needed. This added a days' worth of work to manufacturing, as is had to be created from scratch due to McMaster-Carr only having heavy duty conveyor tensioners.
​
SPRING QUARTER / TESTING:
Testing is conducted during the third quarter of the school year. By this time, construction should have come to a close and the entire conveyance system should be assembled. During the testing portion of this project, the conveyer will be tested, observed, and redesigned based off those observations. The scope of testing will be indicated. To present the results of the project, a website will be published highlighting big topics as well as an attachment of this document. This website will then be presented.
​
The first (intended) method of testing was the speed test. However, due to a motor failure, this testing was not able to be conducted and torque testing had to be done as a result of this failure. This added more time to the project as this prompted a redesign in the way that a new motor had to be assembled and fit into the conveyor design. This added around 3.75 hours to the overall time spent and postponed speed testing for an entire week. Clearly, this did not go as planned... but quick thinking led to torque testing being completed on time and presented to the class. Another obstacle that was run into this quarter was the lack of materials available in the machine shop which led to spending extra time searching for the tools that were needed to conduct the test. This added about a half hour to the testing time.

Figure 5.1. Schedule for Senior Project
Budget
Parts:
The most expensive purchase for the conveyer assembly were the 4-bolt ball bearings, the two head pulleys and the keyway broach set. Although the broach set is not a component for the conveyance system, the purchase was necessary to create a pulley with a keyway due to McMaster-Carr having 6–7-week arrival times. Some of the parts that didn’t have much of an effect on the budget were the roller mounts, fasteners, key stock, spider, etc. In total, parts and tools purchased for this project totaled $1,030. After shipping and taxes the total for parts was $1,176. The budget for parts can be found below, in Table D1. This table details parts identification, description, quantity, and cost.
Outsourcing:
Some components on the conveyer were not able to be found online due to dimension constraints, functionality, or design complications. This led to outsourcing and using the CWU machine shop. Things that were done in the machine shop involved machining the coupler, cutting thin sheet metal plates, machining keys, broaching keyways, etc. This was estimated to be about $100.
Labor:
Majority of the labor involved with this project has to do with assembly with a small amount of machining. While trying to avoid as much machining as possible, it was inevitable for some of the components of the conveyer. Some parts for the conveyer did not align with standard sizes commonly found to order online. Such as the step-up coupler and the head pulley with keyway. Labor costs are associated with tasks for this project in the Gantt chart above in the schedule section. For this, it was assumed that labor wage was $20. The total estimated costs for labor in the first quarter (design phase) is estimated to amount to $1,125. After winter quarter, this estimation was revised to amount to $1,940 for labor costs. After recording hours and keeping track of the time spent on this project throughout the year, the total cost for labor totaled $2225.
Estimated Total Project Cost:
The total project cost totals up to $3,501. Labor costs are estimated to be $2,225, parts costs are around $1,176, and the cost of outsourcing for machining at CWU is about $100.
Sponsor:
This project is sponsored by the Joint Center for Aerospace and Innovation.
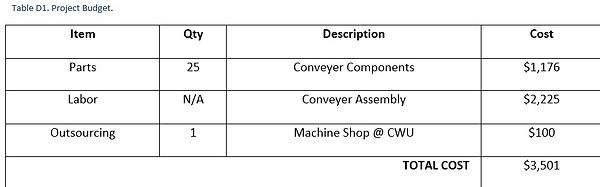